Vacuum Casting
Using Xnparts vacuum casting, each casting has precision and durability. Small quantities of production-grade quality parts can be delivered within 7 days.
Vacuum Casting Factory
We offer a complete turnkey solution for creating master models and cast copies from your CAD designs. Not only do we make high-quality molds, we also provide a full range of finishing services, including painting, sanding, pad printing, and more. We will help you create parts for showroom quality display models, engineering test samples, crowdfunding campaigns, and more.
Polyurethane vacuum casting may be the ideal solution for you. Xnparts’ vacuum casting services are known for producing showroom quality display models, engineering samples, crowdfunding prototypes, and more. Of course, all your parts are professionally painted, printed, and finished for a high level of craftsmanship.
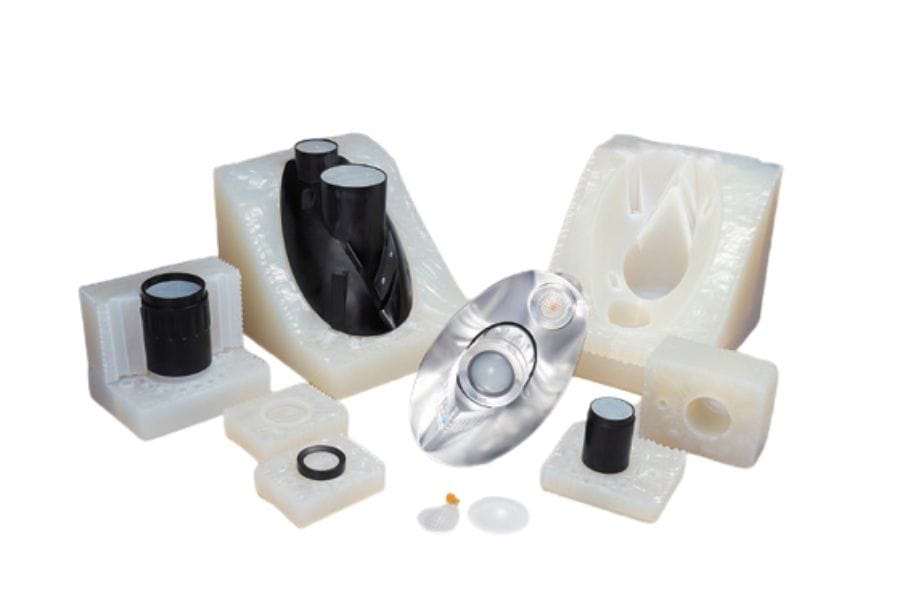
Xnaprts Strong Vacuum Casting Service Capabilities
At Xnparts, we enhance polyurethane vacuum casting by ensuring a minimum dimensional shrinkage of +0.15% for parts under 30 inches, thereby maintaining tight tolerances for complex designs. Our services are highly customizable to meet the needs for transparent, color-matched or special finished parts such as those requiring EMI shielding. We also integrate a variety of inserts into the casting process for enhanced functionality.
Xnparts’ vacuum casting services offer a reliable alternative to injection molding, bridging the gap between prototype development and full production with low costs and long lead times. This provides a cost-effective, quality-assured solution for specific customer needs.
As your reliable vacuum casting manufacturing partner, we provide comprehensive, all-in-one services. Our experienced engineering team not only guides you through the implementation of your entire project, but also provides advice on the optimal component design and its adaptation to vacuum casting manufacturing.
We offer a wide range of plastics to provide multiple possibilities for your application. In addition, we provide high-quality post-processing to ensure that your parts are exactly as you require.
Our ordering process is simple and efficient, allowing you to quickly and easily turn your project into reality. Just upload your drawings or send them via email. Typically, you will receive your personalized quote as soon as the next day.
From Prototyping to Production
Vacuum casting is the perfect method for producing high-quality prototypes and limited-edition parts for a variety of uses. Xnparts can help you achieve your manufacturing goals.
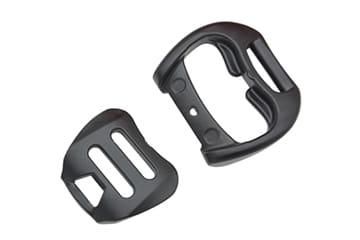
Prototyping
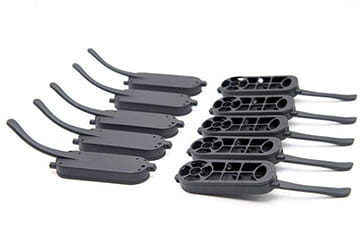
Market Testing
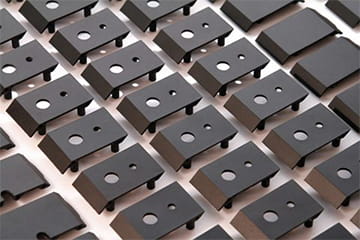
On-Demand Production
Ask us about vacuum casting
For more information about vacuum casting, please feel free to contact us. Your customer support partner will contact you directly to answer any questions you may have.
Vacuum casting technical specifications
Accuracy | Highest precision to reach ±0.05 mm |
Maximum Part Size | +/- 0.025 mm +/- 0.001 inch |
Minimum Wall Thickness | 1.5mm~2.5mm |
Quantitites | 20-25 copies per mold |
Color and Finishing | Color and texture can be customized |
Typical Lead Time | Up to 20 parts in 15 days or less |
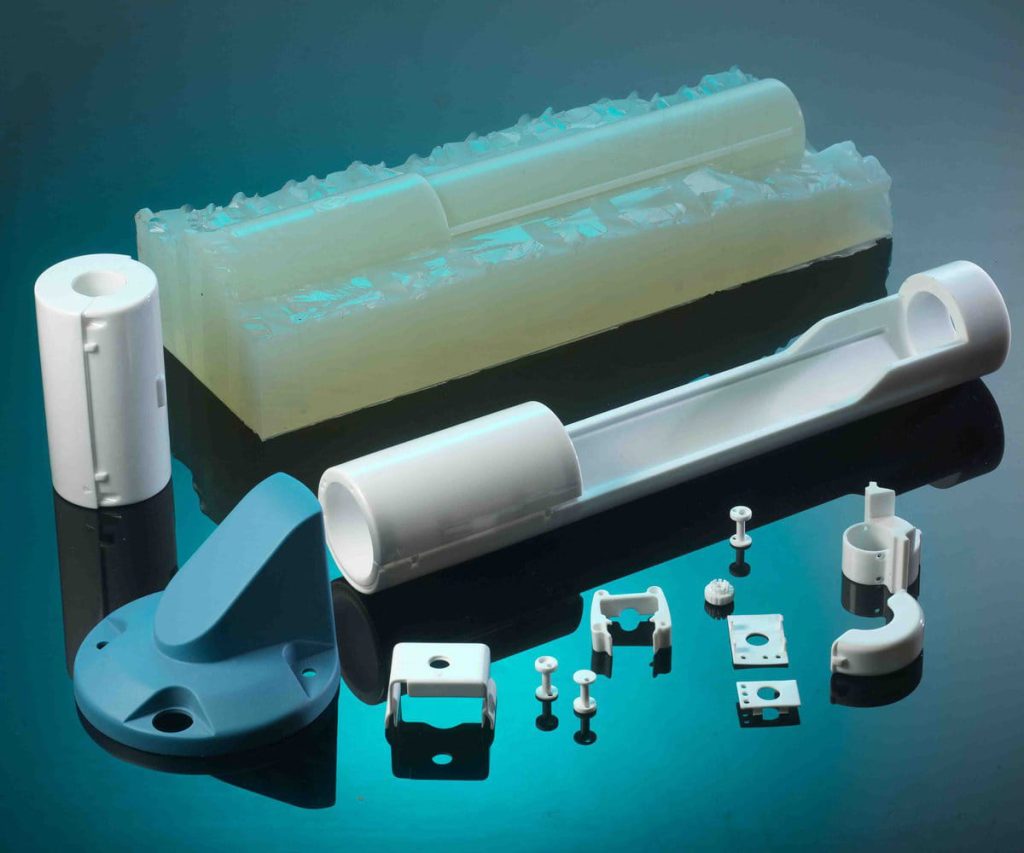
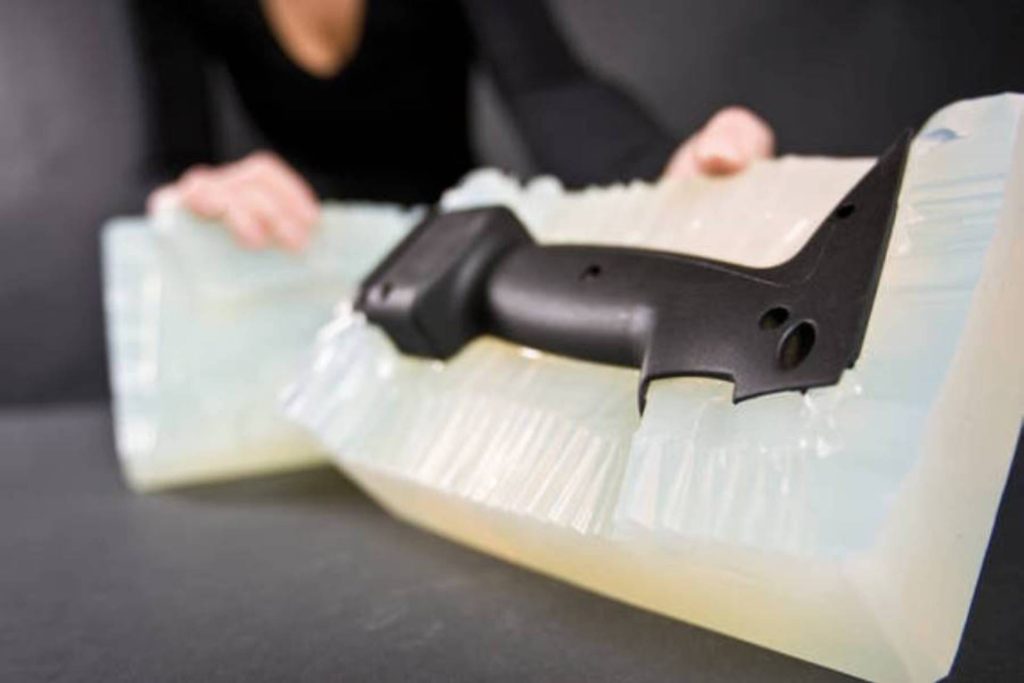
When to Use Vacuum Casting?
Product developers choose vacuum casting when they need to produce high-quality plastic parts in small quantities (10 to 20 pieces) while avoiding the long lead times and financial investment of manufacturing plastic injection mold tooling.
These parts are used for prototypes and display models, crowdfunding and trade show campaigns, testing the fit and function of new designs, and as a bridge to larger volume production. Vacuum casting can also be used for end-use parts in certain applications, as castable casting resins can effectively mimic the properties of ABS, nylon, PP, acrylic, and soft TPE rubbers.
What Materials We Offer
Xnparts’ Vacuum Casting Prototyping service utilizes 3D printed models as master patterns for vacuum casting. We offer ultra-fast delivery times, making this process ideal for experimental design and development processes.
Our unique approach allows for simultaneous multi-color casting and combining a variety of casting materials in a single mold. We offer a wide range of material options, from ABS- and PP-based polyurethane-based materials to acrylic-based epoxies and adjustable hardness elastomers. Whether blending with light diffusers or GFs, or color matching, we tailor our services to your specific requirements.
The materials used for vacuum casting can simulate the following production materials and properties:
- Rubber: High flexibility
- ABS: High rigidity and strength
- Polycarbonate and PMMA: Impact resistance, translucent, high temperature resistance
- Polypropylene and HDPR: High elasticity
- Polyamide and glass-filled nylon: High rigidity
- Filled ABS: Fire resistance, flame retardant
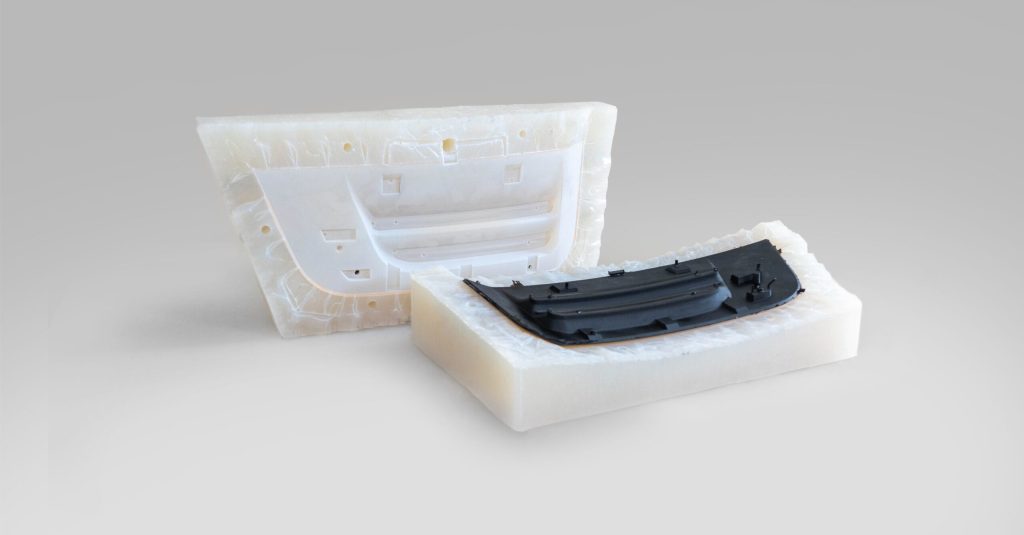
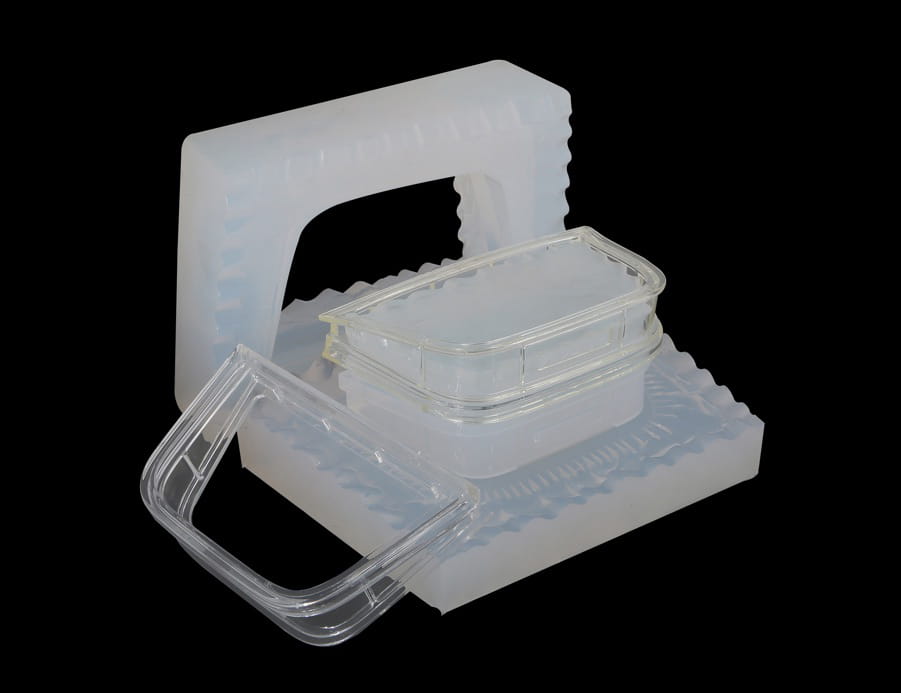
Finishing
Vacuum cast parts can be rigid, flexible, or even rubber-like, depending on the type of polyurethane used. We offer polyurethane in a variety of colors: clear (standard), black, and color-matched. Parts can also have standard, smooth, or custom finishes, including added hardware mounting and painting. If a surface finish is required, such as SPI and VDI surface textures, it is best to CNC machine the master model and finish it. By spraying or painting the master model, we can produce surface textures such as gloss and matte. The finish depends on the post-processing of the component. Sometimes it is limited to the exterior because certain internal aspects of the design cannot be touched.
What is Vacuum Casting?
Vacuum casting, or polyurethane casting, is a versatile vacuum technique that draws liquid material into a mold to create plastic and rubber parts.
The process excels at quickly producing complex, precision components, making it ideal for early quality checks and accelerated product development. Vacuum casting is suitable for small to medium-volume production, with similar precision to injection molding, but at a lower cost and with a faster turnaround time.
Utilizing silicone rubber molds made from a CNC or SLA master model, it can replicate fine details and textures, ensuring consistency and a high-quality finish on every part.
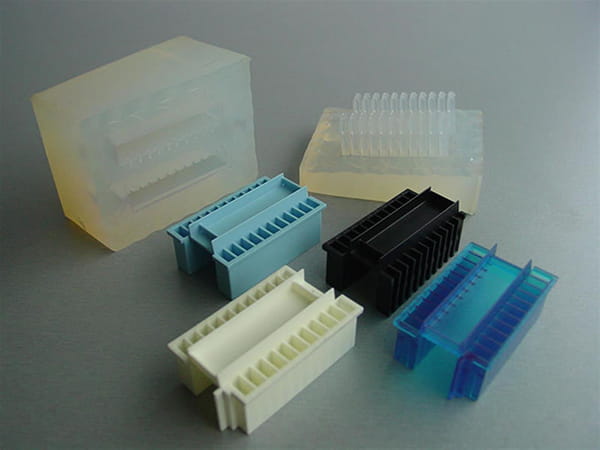
Advantages of Vacuum Casting
- Low mold cost
- Molds can be made in a few days
- Many types of polyurethane resins can be used for casting, including overmolding
- High precision of mold replicas and excellent surface texture
- Molds can be used 20 times or more
- Ideal for engineering models, samples, rapid prototypes, production bridges
Applications of Vacuum Casting
The vacuum casting process is ideal for parts that require high quality, precision, and the performance characteristics required for production parts. We use custom formulated premium polyurethanes to produce the highest quality custom cast polyurethane parts and can also prototype them according to your drawings or sketches. The vacuum casting process and relatively inexpensive tooling make any design changes easy and economical. The vacuum casting process can produce medical devices, housings and casings, sports equipment, low-volume production parts, cases and covers, and prototypes. Some industrial applications for vacuum casting include:
- Engineering models
- Marketing test samples
- Pre-production runs
- Test prototypes
- Rapid prototypes
- Bridge to production
- Production of display parts
- User evaluation
- Consumer testing
- Low-volume manufacturing
- Concept models
- Sales samples
Industries We Serve
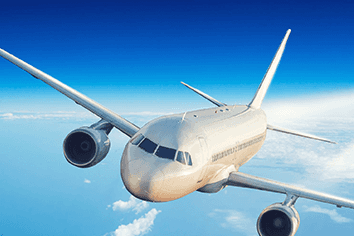
Aerospace
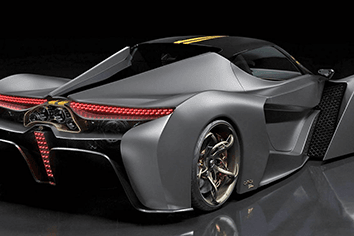
Automotive
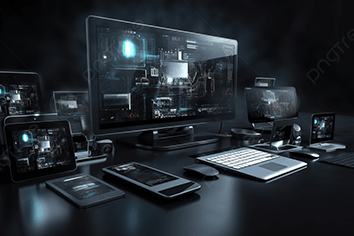
Electronics
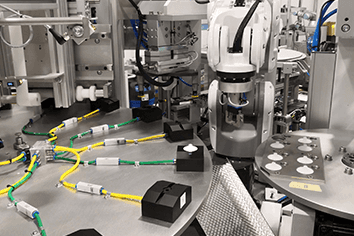
Industrial Equipment
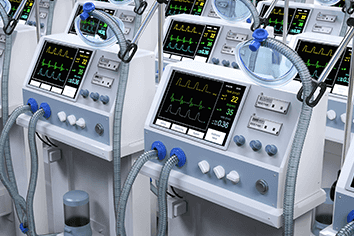
Medical and Dental
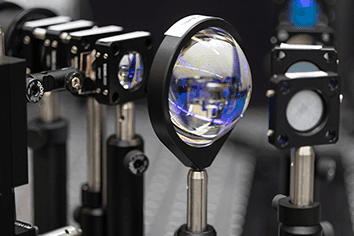
Optics
Request a Free Vacuum Casting Quote Now
Upon receiving your drawings, our engineers will immediately analyze your custom vacuum cast parts. We proactively work with you to clarify all details and then provide a quote that is both economical and accurate.