Overmolding
We focus on providing high-quality overmolding services and provide you with comprehensive options. Our experienced and professional team provides design assistance and material selection guidance to help customers optimize the cost, performance and manufacturability of their overmolding projects. We are committed to providing excellent results that meet or exceed your expectations.
Global Manufacturing Partner for Overmolding Solutions
Xnparts is a custom parts manufacturer that offers a full range of overmolding services from prototypes to full production. Our highly skilled team provides affordable custom overmolding solutions for your parts. We are able to help design and manufacture tooling while assisting with product design and production. We also offer services such as prototyping, assembly, product graphics, custom packaging and shipping. We provide excellent quality control for high volume orders and are able to customize our quality assurance program to meet your specific requirements. In addition to quality control, every aspect of overmolded parts can be customized to produce parts to your specifications. And can assist with affordable tooling design and development, prototyping and more.
With a commitment to innovation, quality and sustainability, we are setting new standards. Our customer-oriented approach makes us a reliable partner to Tier 1 suppliers and OEMs worldwide.
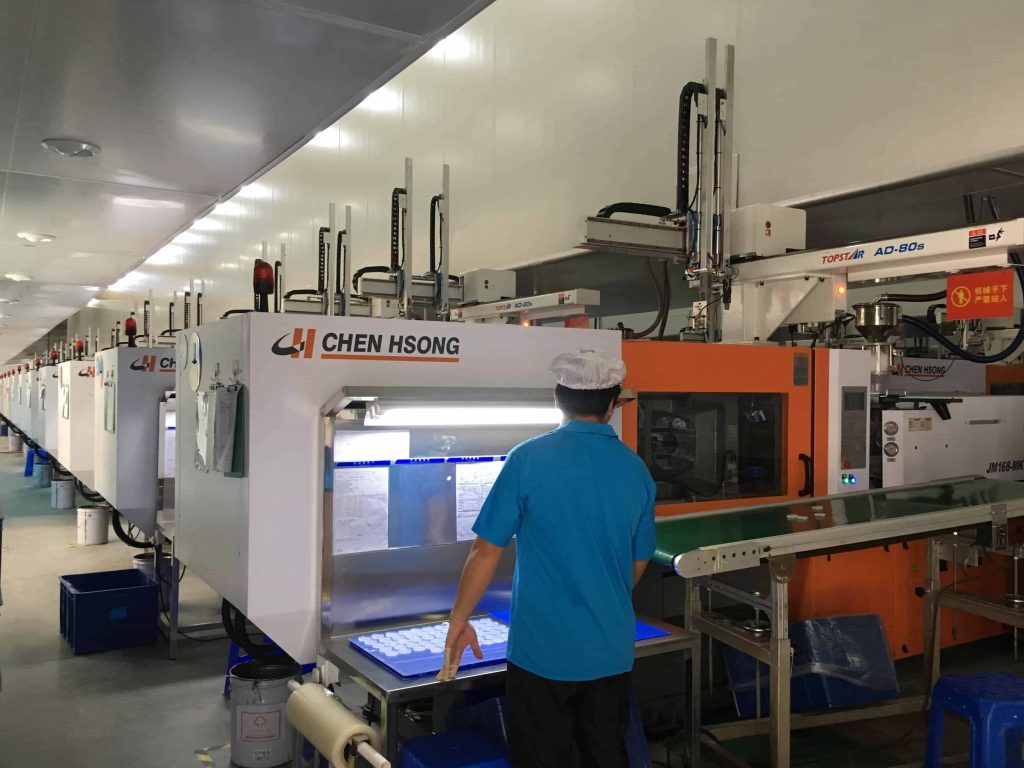
Tolerances in Overmolding Injection Molding
Overmolding Injection molding is a precise process that requires special attention to ensure that the product is manufactured to the correct size, thickness, and diameter. Tight tolerances need to be adhered to when producing overmolded products. At Xnparts, we produce parts with tolerances as small as 0.001 inches. We use efficient machines to produce precise results. Our engineering team is highly skilled and ensures that the products exceed industry expectations. The quality and repeatability provided by our organization is extremely high.
Overmolding Process Types
Xnparts offers a wide variety of injection overmolding services to meet all of your product and engineering requirements. When needed, our overmolding and true two-color molding capabilities allow us to mold multiple materials and colors onto specific portions of an existing part.
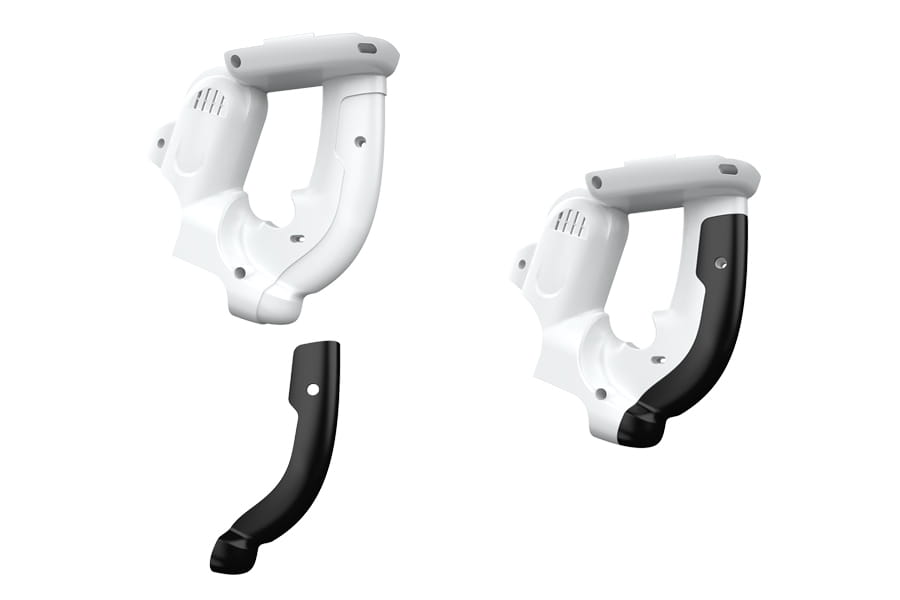
Plastic-on-Plastic
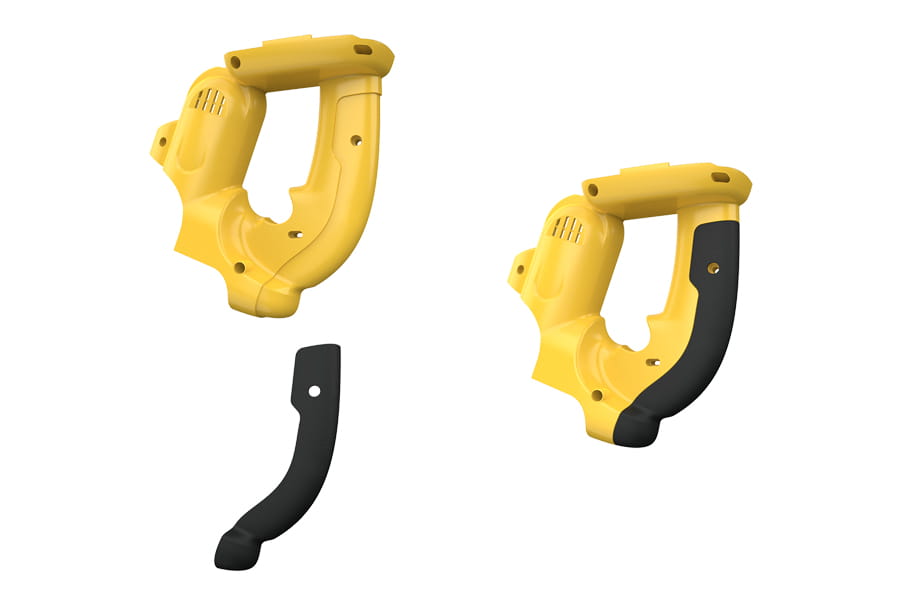
Rubber-on-Plastic
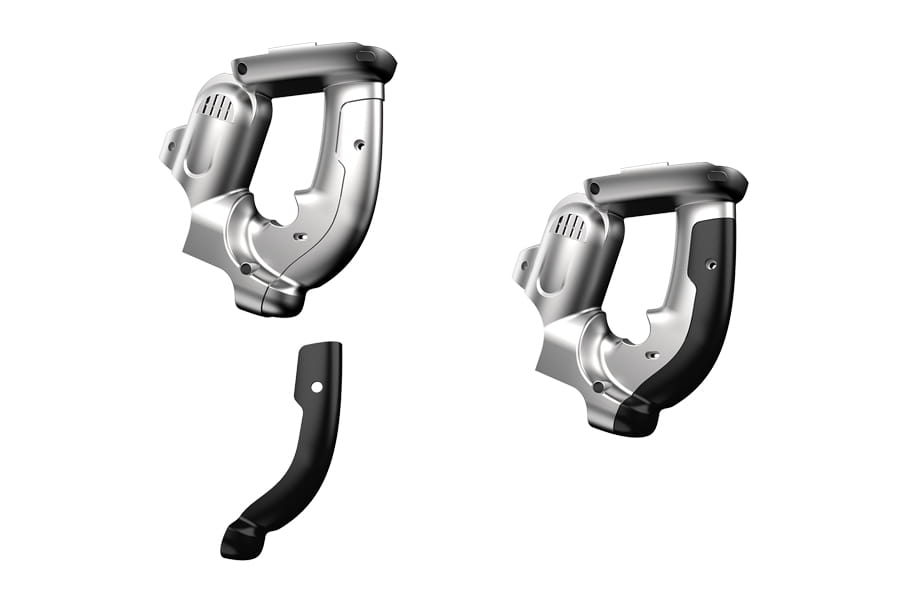
Plastic-on-Metal
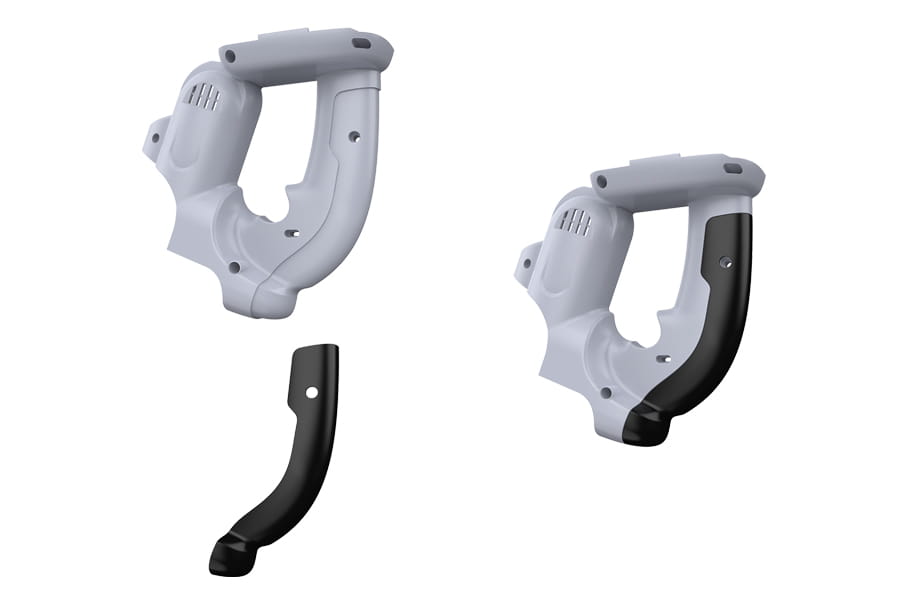
Rubber-on-Metal
Custom Silicone Overmolding Solutions for Your Business
Xnparts’ overmolding and insert molding processes can produce custom prototypes and on-demand production parts in as little as 15 days. We can also provide cost-effective aluminum molds to produce parts using a range of solid silicone rubber and liquid silicone rubber materials.
We work to your timeline and budget. Our cost-effective prototypes can be produced in small batches according to your schedule. We understand and meticulously implement the best strategies to provide your company with high-quality custom silicone baby products.
We specialize in providing excellent quality control for large-volume orders, and we can customize our quality assurance procedures to meet your specific requirements.
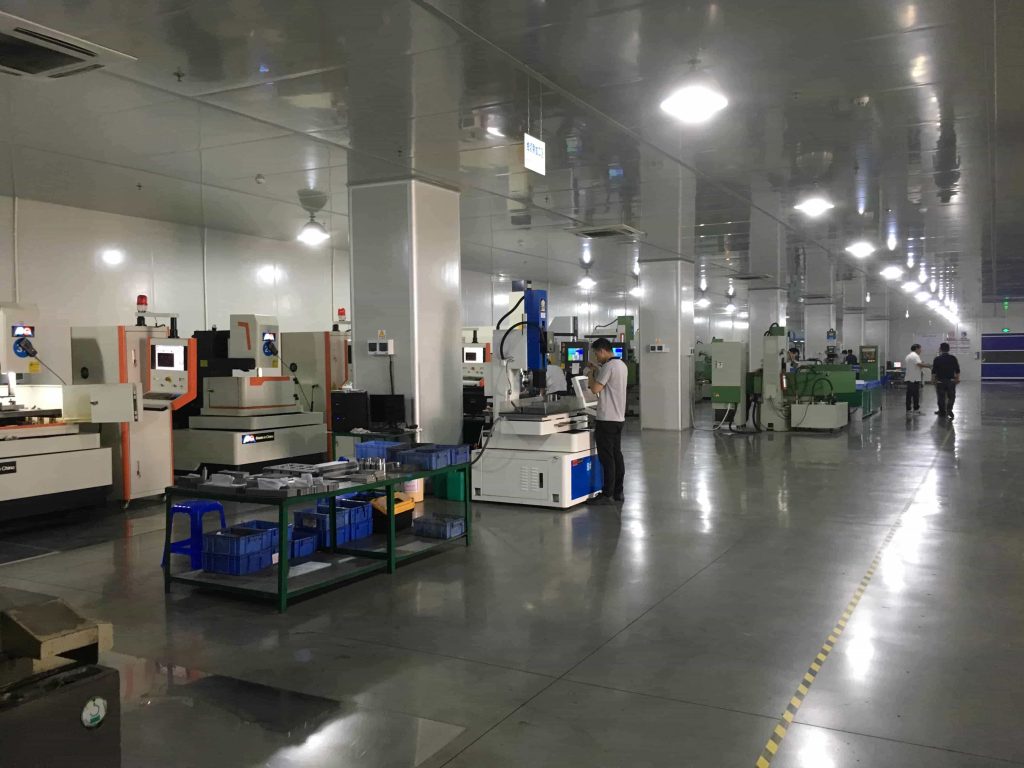
Tooling Services
In-house tooling services, from tooling design to production. Lifetime tooling warranty.
Design for Manufacturability
Quality manufacturing starts with good design. We develop DFM reports to eliminate defects before production begins.
Surface Treatments
Enhance appearance and functionality with a variety of surface treatments, from smooth, glossy coatings to textured or matte finishes.
Assembly Manufacturing
We offer customized assembly services based on quantity and requirements, and we perform manual, semi-automatic or fully automated assembly operations.
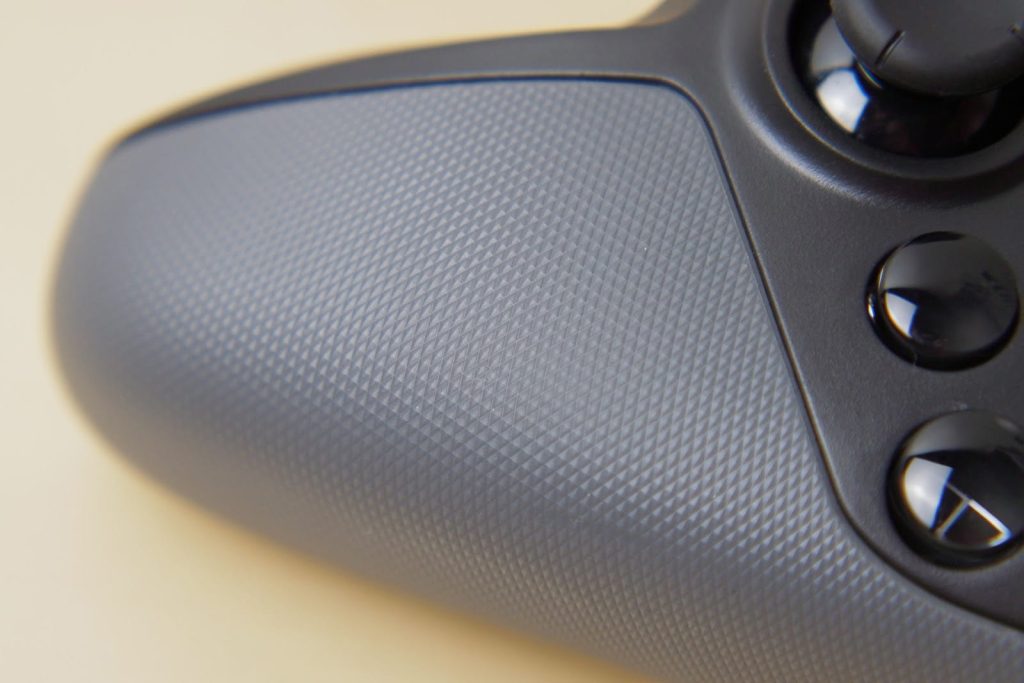
Design for Manufacturability Services
If you have a thoroughly reviewed design, our build-to-spec service is the perfect choice for you. With drawings, specifications, and purchase order requirements, we can start production.
If your project still needs improvement, don’t worry. We will be happy to help you achieve a simpler, more manufacturable design to achieve your goals. Our build-to-spec service can quickly and cost-effectively transform your concept into a finished product. At our company, we believe in customization to meet your specific needs. We only create prototypes when necessary for testing and proof of concept. We always focus on customizing your project to your unique requirements.
Choose Xnparts for your overmolding needs today
Material Options
Overmolding substrate
The most common substrate materials for overmolding are thermoplastics. These materials provide a stable foundation for the overmolded component. The most common substrate materials include:
- Polycarbonate
- Polypropylene
- Nylon
- Polystyrene
- PES
- PEK
- PEEK
- PEI
- Plastic Alloys
- GFRP
Overmolding Bonding Materials
The most common overmolding materials are thermoplastic elastomers, known for their flexibility, elasticity, and compatibility with a variety of substrates. Some other common bonding materials include:
- TPE
- LSR
- TPU
- Nitrile Rubber
- HNBR
- FVMQ
- Acrylic Rubber
- FKM
- Chloroprene Rubber
- NBR-CH
Surface Finish Options for Molded Parts
The following are the surface finish options available from Xnpart. If the finish you want is not listed, please contact us and we will customize the finish just for you.
Standard Finishes
The finish selected by the moldmaker is typically SPI B-2, with internal non-decorative surfaces left as machined.
SPI Finishes
Range from 3-grade diamond/high polish to 320 stone low polish, including SPI A-1 to SPI D-3 finishes.
Molding
No secondary polishing or grinding is required, and parts will retain machining marks.
MoldTech Finishes
Includes matte, swirls, lines and patterns, as well as standard finishes such as MoldTech MT11010, MT11020 and MT11030.
Other Textures - VDI
VDI 3400 finish is primarily processed by EDM and produces fine to coarse matte surfaces.
Assembly
Ability to assemble and mark injection molded parts, discuss specific needs with your salesperson.
Threaded Inserts
Mount standard inserts in UNF and metric sizes.
Pad Printing
Transfer 2D images to 3D parts and perform image review.
Laser Engraving
Engrave part numbers, logos, and more onto your parts.
What is overmolding?
Overmolding is an injection molding method where a layer of plastic, typically a thermoplastic elastomer (TPE) or similar material, is molded over a previously manufactured substrate. Think of it as covering a part molded with hard plastic, seamlessly combining multiple materials into a single part.
The key to overmolding is chemically bonding the cover to the substrate. To achieve this, the two materials should be compatible, which is why the substrate is almost always some kind of polymer resin.
If the overlay and substrate materials are poorly or completely incompatible, the bond between the two will be low. Designers can address this by incorporating mechanical bonds into the substrate, which can include textured surfaces, holes, and undercuts. To achieve maximum strength, engineers design for a combination of chemical and mechanical bonds.
Overmolding is done in two ways: two-shot overmolding and pick-and-place overmolding.
Advantages of Overmolding
- Better chemical resistance: Overmolding can be used to make a main part more chemically resistant so it doesn’t corrode and get damaged.
- Additional functionality: Overmolding can be used to add new features or functions to a main part, increasing its usefulness and value.
- Simplified assembly: Overmolding can help you combine multiple parts into one, eliminating assembly, making manufacturing easier.
- Better performance: Overmolding can be used to make a main part perform better, by adding new materials or features, making it work better.
- Make it look better: Overmolding can make a main part look better. It makes it look beautiful.
- Reduce weight: Overmolding can help you reduce weight. It makes your main part lighter, but still strong and durable. It makes it easier to carry and handle.
- Better heat resistance: Overmolding can be used to make a main part more heat resistant, so it doesn’t get too hot or too cold.
- Stronger and tougher: Overmolding can make your part stronger and tougher, so it lasts longer and performs better.
- Better electrical insulation: Overmolding can be used to improve the electrical insulation of major components, helping to protect them from electrical shock and damage.
- Better appearance: Overmolding can make major components look better. It can make them look more attractive.
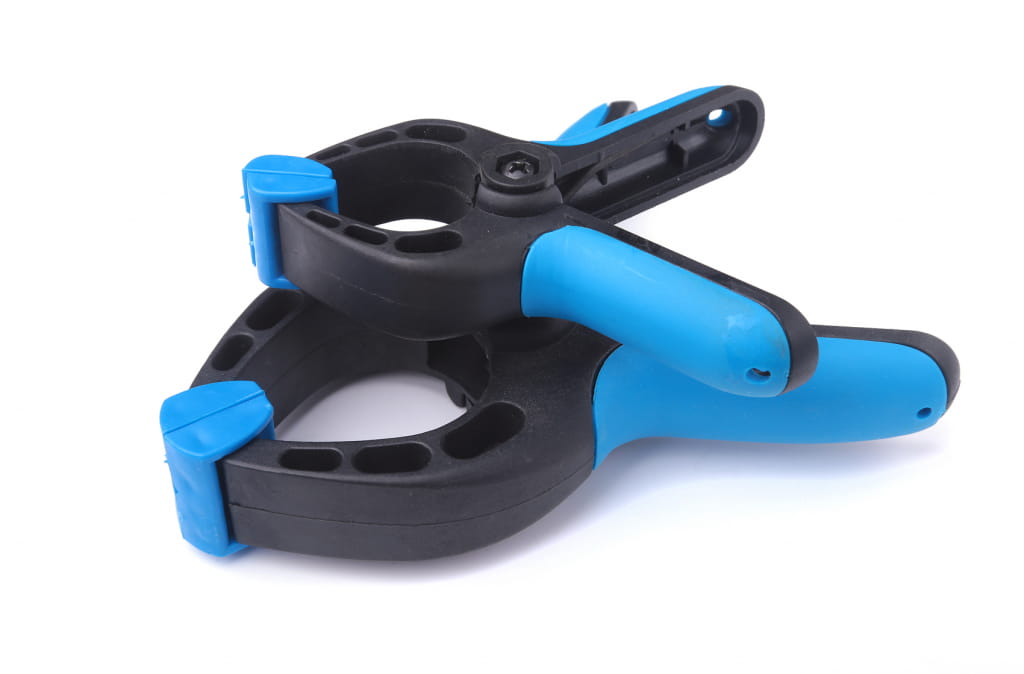
Product Design and Injection Mold Manufacturing Considerations
The primary challenges in developing an insert, encapsulation, or overmolded component are part geometry and mold design. The overmolded substrate must be dimensionally consistent, with particular attention paid to areas that will be sealed during the overmolding process. Typical tolerance requirements for these features are within ±0.001”, with the exception of softer substrates, which can tolerate some degree of “squeeze.” The substrate geometry must also be carefully considered to determine how best to seal its surface against the pressures of overmolding, how to support areas that cannot be supported with tool steel, and how to provide optimized gate locations.
Tool Design Considerations
Tool design for overmolding has several specific requirements that should be considered in part design. When an operator or robot places the insert or substrate into the overmolding tool, it needs to be successfully positioned and adequately secured when the tool is closed, and during the injection molding process, the high pressures can displace the substrate. This is critical because failure can result in a scrapped part or even damaged tooling, which is often time-consuming and costly to repair.
If not properly supported, the plastic substrate can be displaced or deformed by the overmolding pressure. To achieve this, the tool needs to be designed to grip the geometry of the insert. This is usually accomplished through features in the tool steel that the insert can rest on and clamp when the tool is closed. Designers need to be aware of this because these support locations will prevent the overmolding material from flowing into these areas, which means they will be exposed in the final part. Care should be taken to design appropriate support features in the substrate that are either hidden or functional in the component.
The design of the seam between the overmolded part and the insert or substrate is also critical so that the tool steel can successfully close to the substrate, preventing overmolding material from flashing outside the intended geometry. Closure works best when the mold closing action can create a small amount of preload or squeeze force on the part to successfully seal the overmold cavity. When the overmold parting line is more dynamic, special attention must be paid to the closing geometry and substrate support in the mold to prevent flashing.
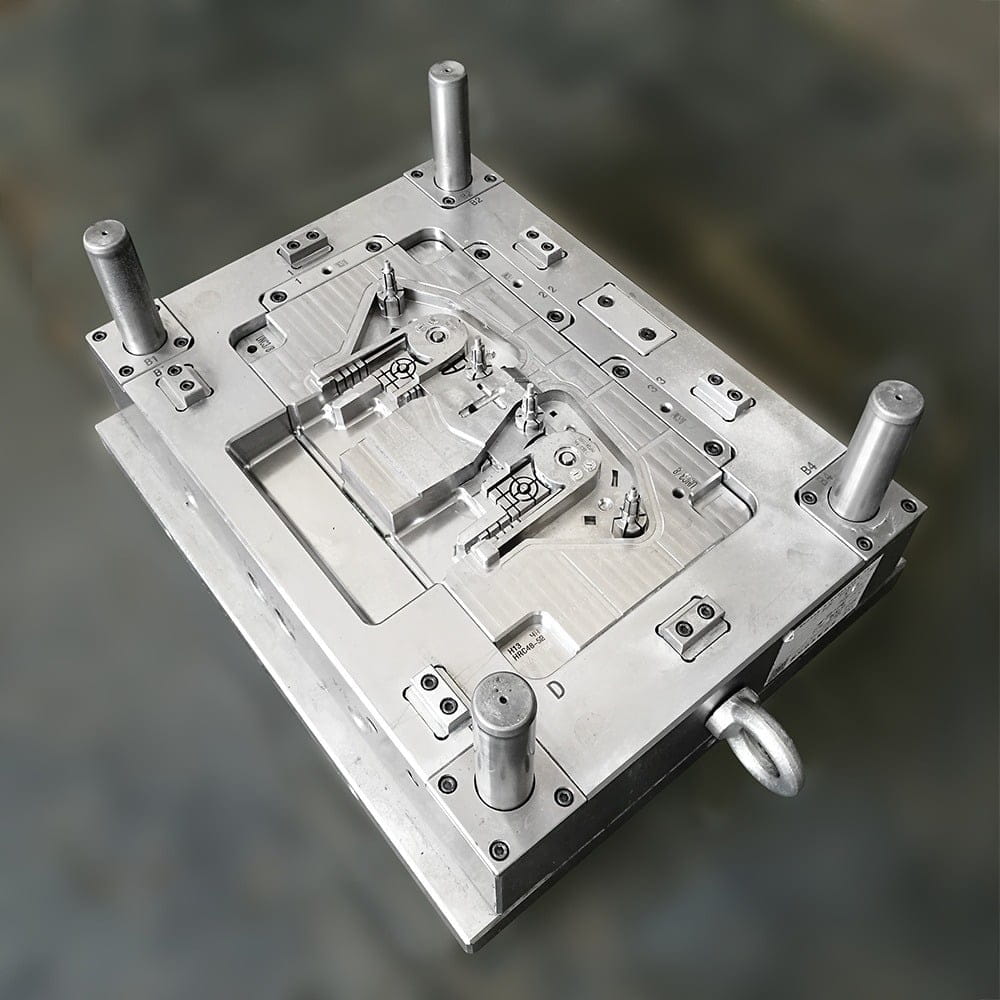
Overmolding Design Tips
- Wall thicknesses between 0.060 in. and 0.120 in. (1.5 mm to 3 mm) generally provide the best bond.
- Keeping corners to a radius of 0.020 in. or at least 0.5 mm reduces local stresses.
- If a part requires a thick TPE section, it should be hollowed out to minimize shrinkage issues, reduce part weight, and reduce cycle time.
- Avoid deep or unvented blind pockets or ribs in the design.
- Use gradual transitions between wall thicknesses to reduce or avoid flow issues (backfill, air traps, etc.)
- The TPE/TPV should be thinner than the substrate to prevent warping, especially if the part is flat, long, or both.
- Overmolding requires mechanical or chemical bonding to the substrate, so the overmolding material should be chosen to achieve this.
What is the difference between overmolding and insert molding?
Insert molding and overmolding may look similar on the surface, but these processes are a bit different.
Overmolding is used to create a part and then place another layer of plastic injection molding material over it. For example, a plastic bicycle handlebar with a soft silicone grip is an overmolded part.
In contrast, insert molding is a process where a pre-molded part (usually metal) is loaded into a mold and then molded into the final part with a special thermoplastic resin. For example, brass contacts can be embedded in a plastic resin to create a plastic electrical connector, or a metal threaded insert can be placed into a plastic housing.
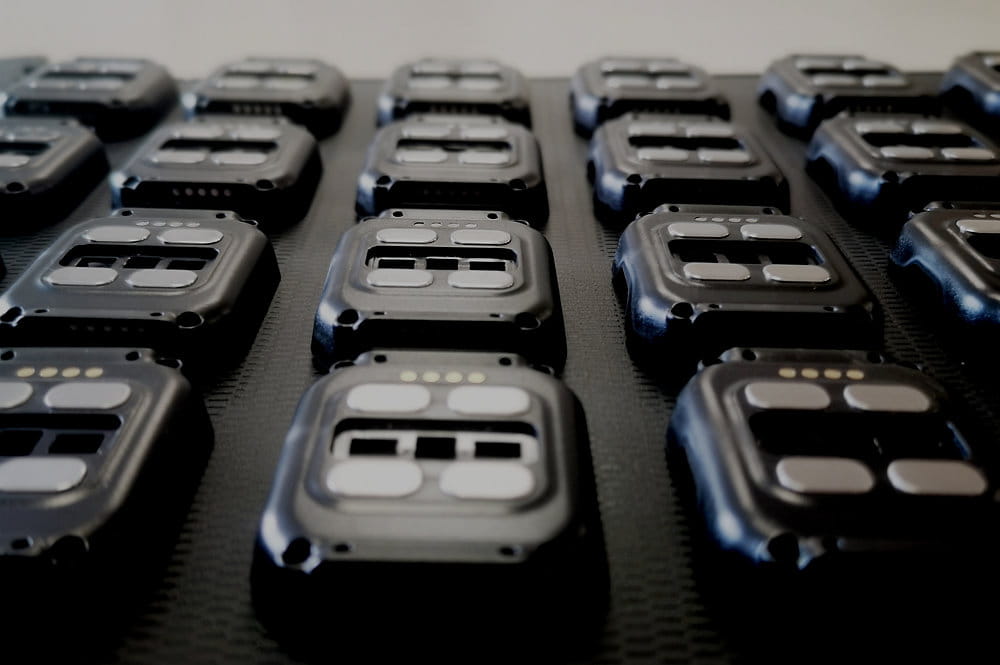
Industries We Serve
Overmolding can accommodate a wide range of material options in various combinations and forms. It can be used for nearly every application you can think of. With the right design, materials, and processes, this technology can enhance the functionality, aesthetics, and durability of plastic parts. Xnparts can help you manufacture plastic products using this method. We have experience using this method to manufacture products for a variety of uses.
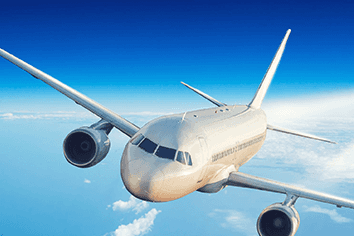
Aerospace
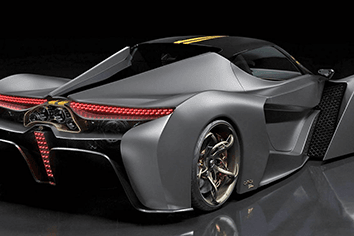
Automotive
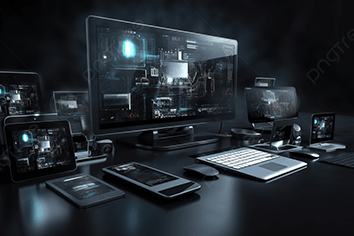
Electronics
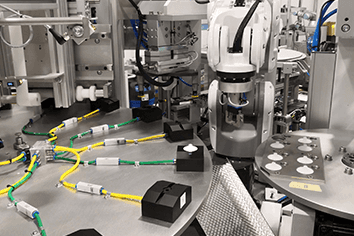
Industrial Equipment
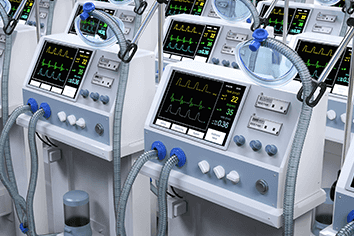
Medical and Dental
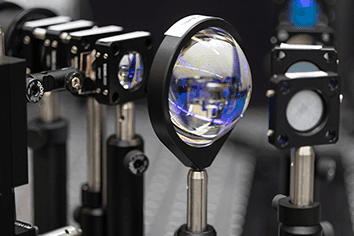
Optics
Let's get started on your new project!
At Xnparts, we offer custom overmolding manufacturing services to meet your specific application needs. From part and mold design to post-processing and quality control, we are your one-stop shop for all your overmolding needs.