cnc turning
If you need a high-quality, precision CNC turned parts manufacturer, Xnparts has you covered. We can take on projects of any size and can produce a wide range of turned parts and assemblies (from metal to plastic materials) to your exact specifications. From small batches to large-scale production, you can trust us to meet all your CNC turning needs.
Is my part suitable for CNC turning?
While there are many factors that determine whether a part can be most cost-effectively manufactured on a specific CNC turning center, some of the factors we look at include:
- How many parts are needed in the short and long term? CNC turning centers are generally suitable for prototypes and short-run production runs.
- What is the maximum outer diameter of the part? For Xnparts’ CNC turning centers, the maximum outer diameter of a chucked (feedable) part is 2.5.”
- Parts with an outer diameter greater than 2.5 inches are chucked separately, depending on volume, which affects pricing.
- Parts with an outer diameter less than 1.25 inches and with moderate to high production volumes may be better suited for a Swiss screw machine.
- If a part can be made on both a CNC turning center and a 32mm Swiss screw machine, factors such as projected production volume and lead time are critical in choosing the best method to use.
Precision Turned Parts Manufacturer
Xnparts works with engineers, designers and procurement teams to consistently deliver CNC turning services on time and on budget. With unrivalled quality, capability and flexibility, our wide range of manufacturing processes and finishing options means we are a one-stop solution for your CNC precision manufacturing requirements. Combined with our responsive, personal and knowledgeable customer service, we can help you move your custom CNC turned parts project forward, from initial consultation through to delivery.
We uphold a culture of quality and perform a variety of supervised and documented testing and inspection procedures at all critical stages of production. Customers can rest assured that parts will not leave our factory unless they meet the highest quality standards.
In addition, we also offer other manufacturing capabilities, including injection molding, CNC milling and 3D printing, to provide our customers with a comprehensive manufacturing solution.
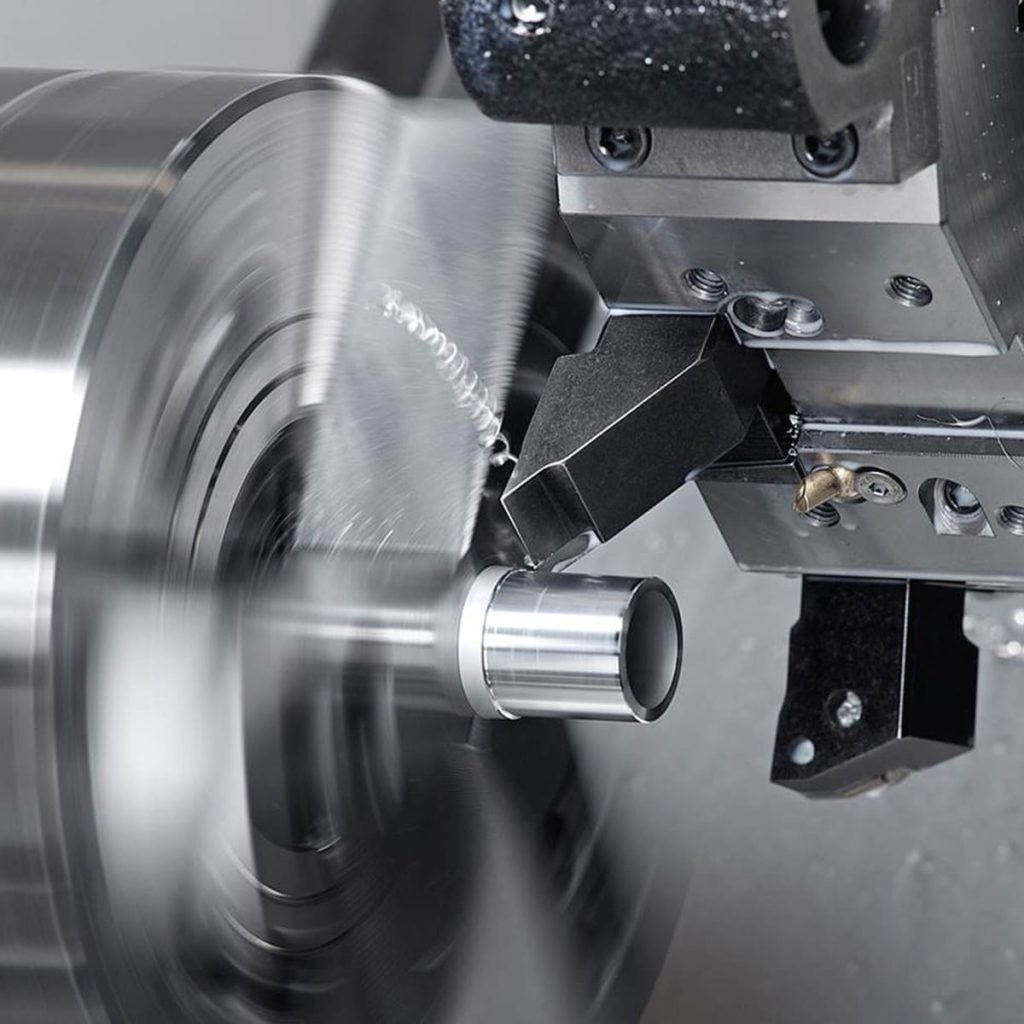
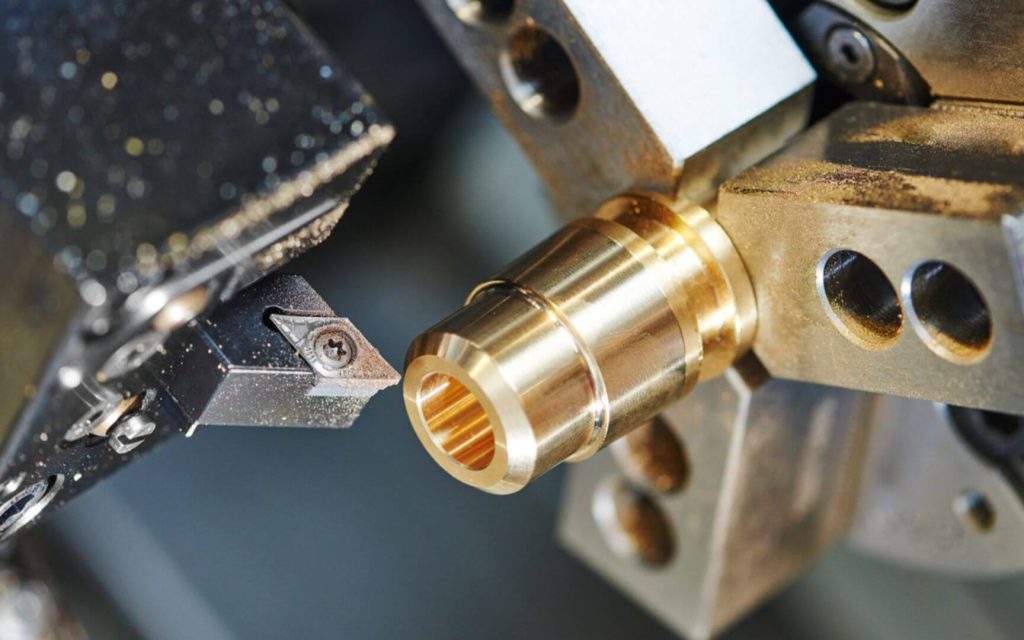
Our Service Capabilities
We use state-of-the-art CNC lathes to produce turned metal parts to tight tolerances for all applications in a wide range of industries. Using metal or plastic bar stock up to 1.25″ OD, we can machine surfaces and planes to tolerances up to ±0.0005″ and feature locations and profiles to ±0.0005″. We also offer DFM services to help speed part production, streamline production processes, and reduce costs. Our engineering team will work with you as needed to optimize your design for improved manufacturability without changing the fit, form, or function of the turned part.
Our Quality Assurance
The company has a strict quality control system to ensure that all products meet customer requirements. Before delivery, we thoroughly test our customers’ products to ensure that they meet specifications, including dimensional accuracy, surface finish, hardness and precision.
We utilize computerized measuring equipment to verify critical dimensions, ensuring that every product we produce is of the highest quality.
Our commitment to quality ensures that every customer receives their products on time, with the highest accuracy and in accordance with their requirements.
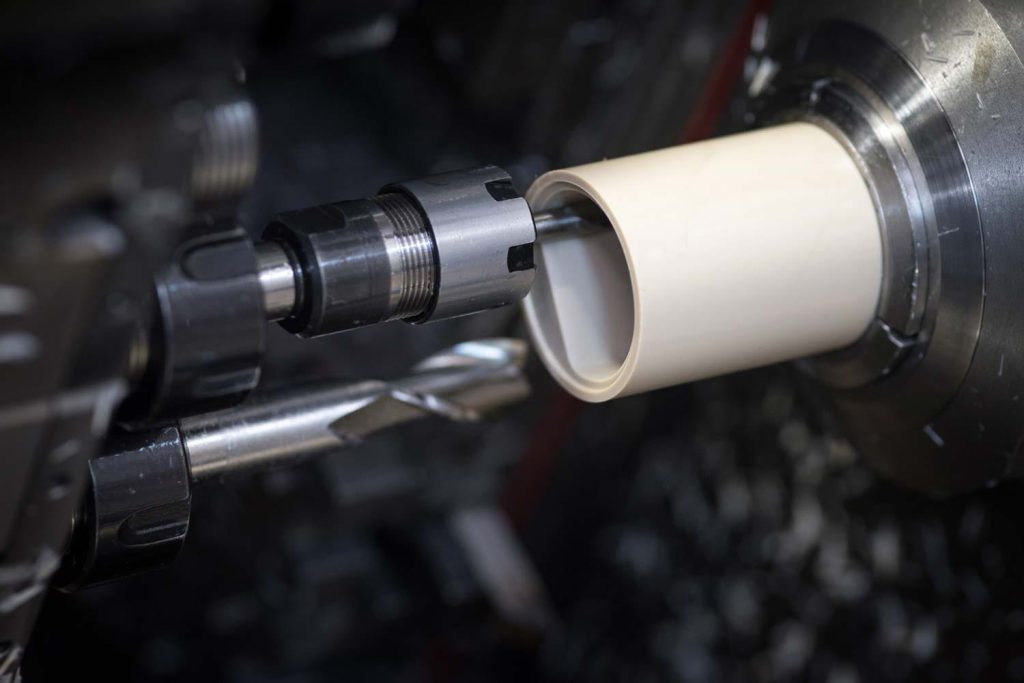
Ready to start your CNC turning quote?
Types of CNC Turning Processes
Cylindrical Turning
This is a process that uniformly reduces the diameter of the workpiece to prevent variations in the cutting diameter.
Taper Turning
Taper turning is the process of machining a workpiece with a reduced diameter into a cylindrical shape.
Grooving
Grooving is a CNC turning process that forms a narrow cavity by pressing a forming tool into the workpiece.
Parting
Parting is the process of removing the entire workpiece from the original workpiece by planing.
Spherical Forming
The process of creating a shape around a fixed axis with the help of a program, reducing the diameter to zero to obtain a perfect spherical shape.
Knurling
The knurling process is the process of cutting the workpiece into a serrated shape. It is used for materials that require extra grip.
Threading
Threading is a CNC turning process. It helps in making grooves that allow the workpiece to be easily screwed into other objects.
Boring
A single-point tool is fed linearly in a direction parallel to the axis of rotation, machining the inner diameter of an existing hole in the part.
One-stop solution
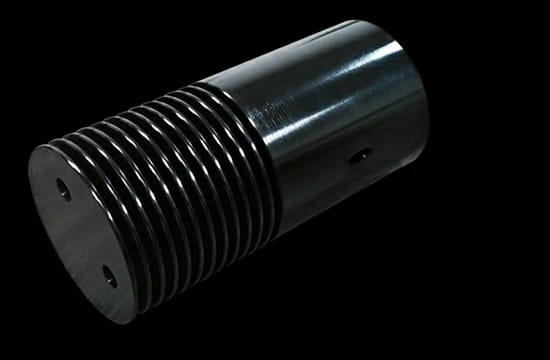
Rapid prototyping
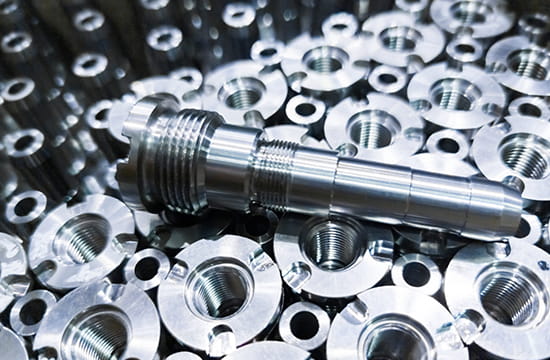
Production
What types of parts are suitable for CNC turning?
- CNC turning is suitable for making high-precision parts. Due to the high manufacturing precision of CNC lathes, workpieces with precise tolerances can be processed, sometimes reaching a tolerance of 0.001mm.
- CNC turning is suitable for making parts with complex shapes. Any plane curve can be approximated by a straight line or arc. CNC lathes have arc interpolation functions.
- CNC turning is suitable for small and medium-sized batches of parts of various varieties.
- CNC turning is suitable for processing parts with high surface roughness. Generally, the roughness of CNC turning can reach Ra6.3.
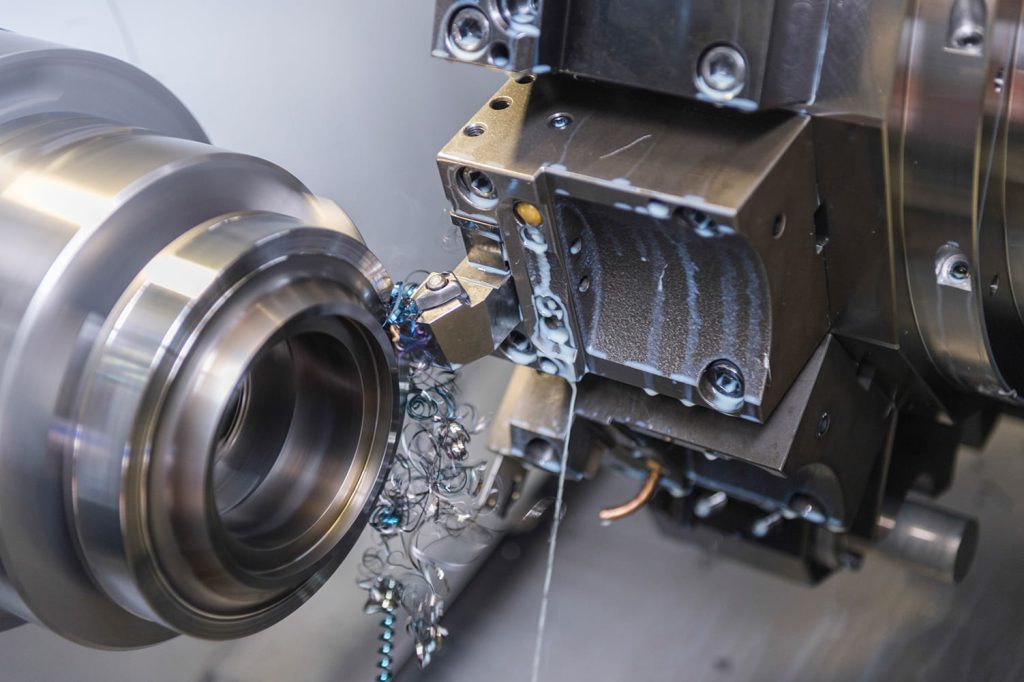
CNC Turning Material Options
We work with a wide variety of composite and metal materials. You have a variety of options for your application depending on the properties and characteristics required for the part. We have experience processing the following materials:
Metals
- Aluminium
- Mild steel
- Stainless steel
- Brass
- Titanium
- Magnesium
- inconel
- Tool Steel
- Steel Alloy
- Bronze
Plastics
- ABS
- PEEK
- Nylon (PA)
- POM (Delrin/Acetal)
- Polyethylene (PE)
- Polyvinyl chloride (Pvc)
- PMMA (Acrylic)
- PTFE (Teflon)
- PPSU
- PS (HIPS)
- Polyethylene Terephthalate (PET)
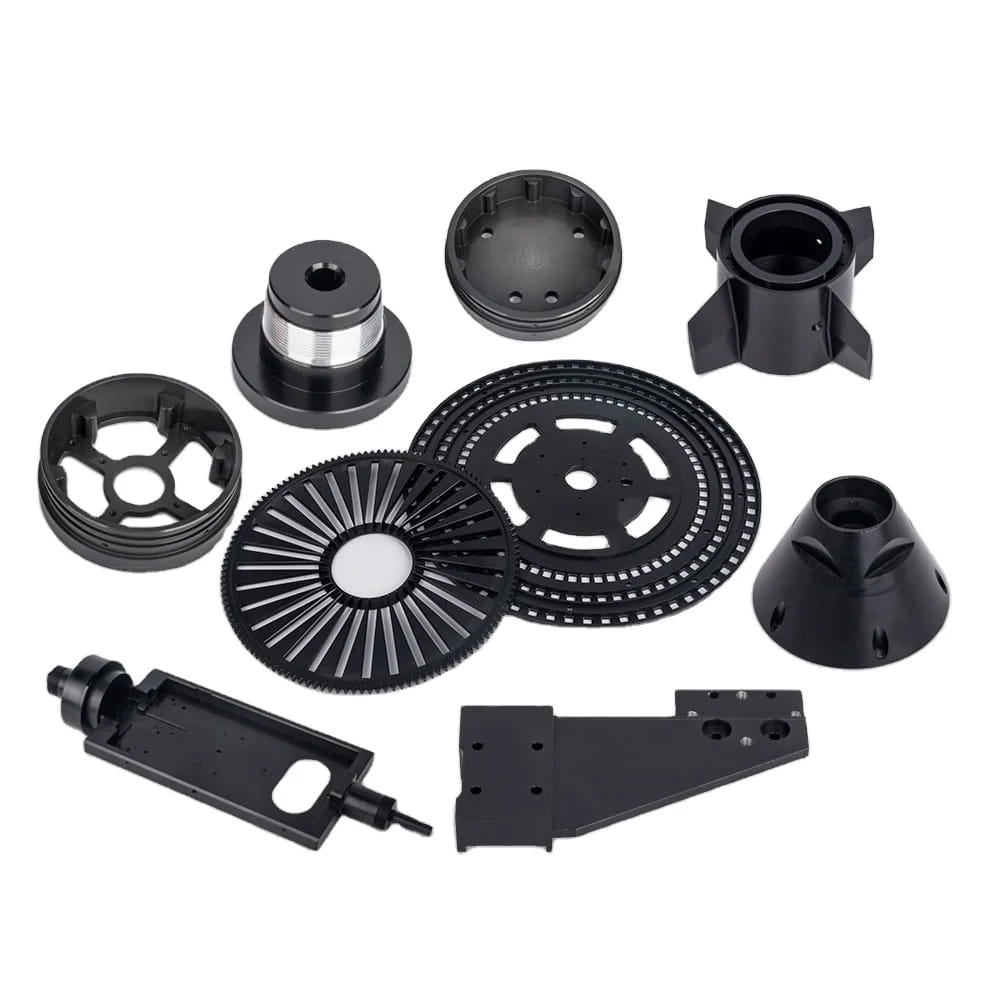
Surface Finish Options for CNC Turned Parts
Xnparts offers a wide selection of surface treatments to improve the surface quality of CNC turned parts. Surface treatments applied after machining can change the appearance, surface roughness, hardness, and chemical resistance of the parts produced.
- As machined (Ra 3.2μm / Ra 126μin)
- Smooth machining (Ra 1.6μm / Ra 63μin)
- Fine machining (Ra 0.8μm / Ra 32μin)
- Polishing (Ra 0.8μm / Ra 32μin)
- Bead blasted
- Brushed + Anodized type II (Glossy)
- As machined + Anodized type II
- Chromate Conversion Coating
- Black oxide
- Electroless Nickel Plating
- Bead blasted + Anodized type II (Matte)
- Bead Blasted + Anodized type II (Glossy)
- Brushed + Electropolished (Ra 0.8μm / Ra 32μin)
- As machined + Anodized type III (Hardcoat)
- Brushed (Ra 1.2μm / Ra 47μin)
- Powder coated
What is CNC Turning?
A CNC lathe is a numerically controlled machining technology that also uses computers and 3D drawings or prints to guide the geometry of parts made using different types of subtractive machining processes. In the case of turning, the workpiece is clamped in a chuck and rotated while a cutting tool is fed into the workpiece to remove material. The tool is programmed to trace the outer and inner shape of the part to create the desired geometry.
The material itself is fixed to and rotated by the spindle, while the cutting tool can move along multiple axes. The types of parts that CNC lathes make are typically cylindrical or symmetrical about an axis.
Benefits of CNC Turning
CNC turning offers numerous benefits, making it a top choice for many industries. Here are some of the key benefits of CNC turning:
- Precision and Accuracy: CNC turning ensures precise production of complex parts that meet tight tolerances and exact specifications.
- Efficiency and Productivity: Automated operations in CNC turning increase efficiency and productivity, reduce production time, and minimize human intervention.
- Versatility: CNC lathes can process a wide range of materials and produce a wide range of parts, making them suitable for a variety of industries.
- Consistency and Repeatability: CNC turning provides consistent and repeatable results, ensuring consistency and interchangeability of parts.
- Flexibility and Customization: CNC turning allows for rapid adjustments, prototyping, and customization, enabling rapid response to design changes and customer requirements.
- Complex Geometries and Intricate Features: CNC lathes can create complex features and complex geometries that are difficult to achieve with traditional methods, expanding design possibilities.
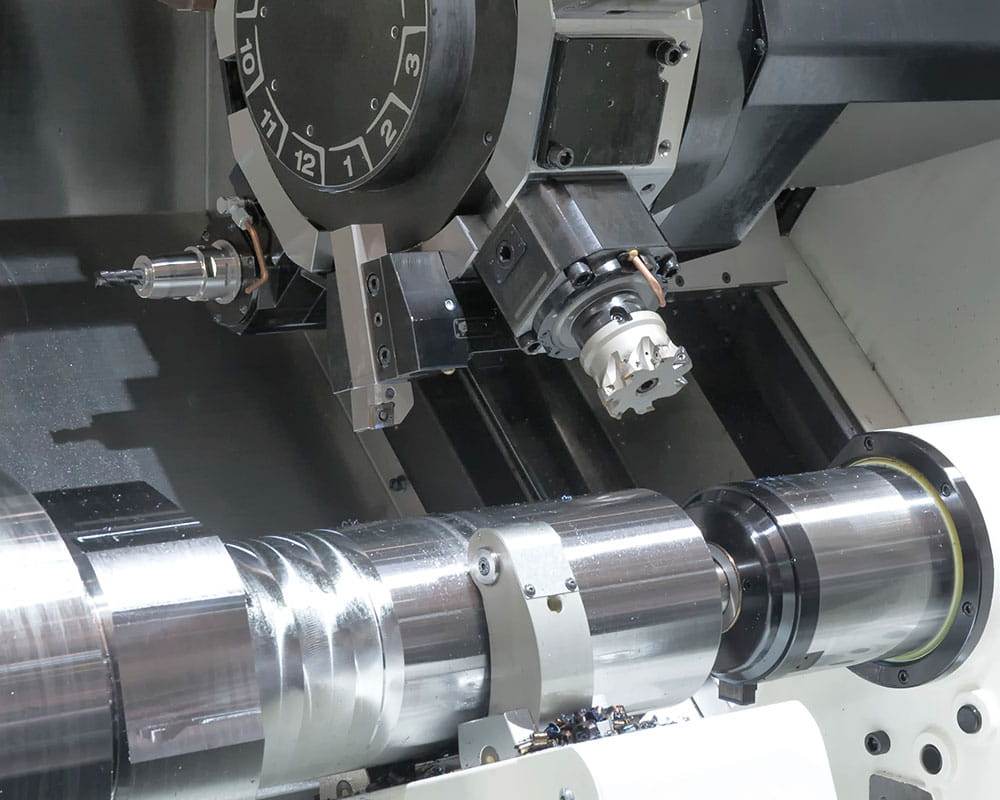
Differences between CNC Turning and Milling
If you understand how turning works, then it is easy to understand how milling works; because the two are completely opposite. In turning, the tool moves linearly and the part rotates; but in milling, the tool rotates and the part moves linearly on the X and Y axes of the table. In the case of milling, the Z axis is the vertical axis of the tool. This is their fundamental difference. But it is not their only difference.
In CNC turning, single-point cutting tools are usually used; this is why turning is a “continuous cutting” process. On the other hand, milling tools (such as router bits, end mills, etc.) are multi-point cutting tools; in other words, they have multiple cutting edges. Therefore, the milling process is theoretically an “interrupted cutting” process.
You should also understand the primary and secondary motions. The primary motion is always a rotational motion, while the secondary motion is a linear motion, i.e. the feed rate. This means that in CNC turning, the primary motion is in the part and the secondary motion is in the tool. In CNC milling, the primary motion is in the tool and the secondary motion is in the part!
Industries We Serve
We offer a wide range of designs at competitive prices and meet the stringent quality and delivery requirements expected by a variety of industries.
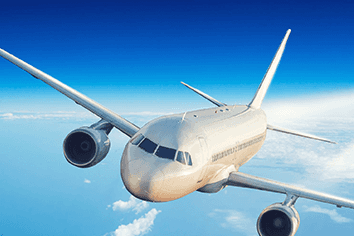
Aerospace
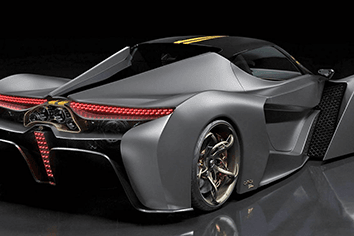
Automotive
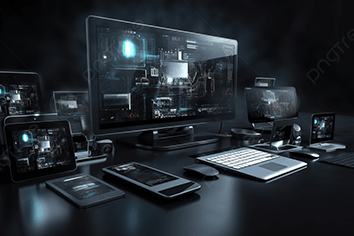
Electronics
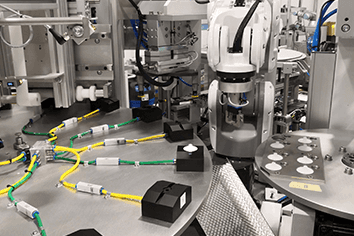
Industrial Equipment
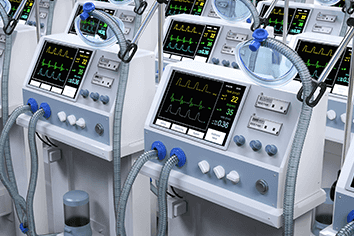
Medical and Dental
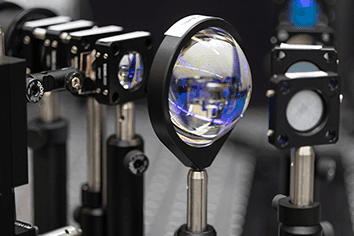
Optics
Are you trying to find the right machine shop to do the job?
Whether you need a single part, a prototype, or large-scale production, Xnparts can provide you with cost-effective CNC turning services for all your lathe machining needs. Our turning processes are economical for both long- and short-run production runs, and our team of machinists are able to create parts with a wide range of hole depths while maintaining tight tolerances and a smooth surface finish. Contact us today.